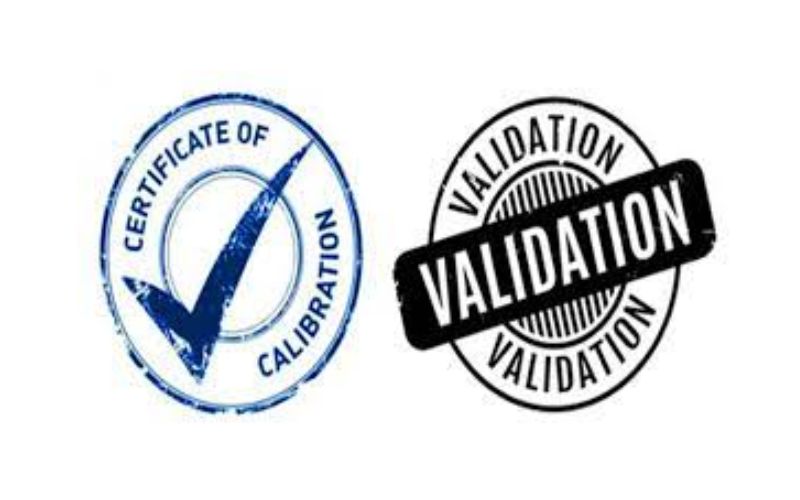
Validation VS Calibration
The FDA first established the idea of validation in 1979 in an effort to raise product quality.
Validation is documented evidence that provides the confidence that a process will consistently result in a product with the pre-specified requirements and quality. It is a process, procedure, or action that must be validated in writing to show that it will yield the same outcomes in testing and production.
In the pharmaceutical sector, validation ensures that a product created is of high quality, and suitable for use and that the same product will be generated when following the precise stated processes or procedures again.
On the other hand, calibration is the process of calibrating an instrument or equipment to show that the data it produces is within the tolerances of the reference unit. The device’s accuracy, range, and precision are determined by calibration.
VALIDATION
Validation is the documented evidence that demonstrates the end product will be of the same quality when we adhere to the detailed specified procedure.
Validation guarantees the same outcomes.
A verified assurance that each part or component of the
A validation protocol is used to perform the validation.
When there are no standards available, validation is done.
Validation is frequently used for processes and procedures.
Validation is done in the ways listed below.
- Process Modification
- Change in Approach
- Formulation modification
There are no reference standards available for comparison in validation.
The pharmaceutical industry’s validation team performs validation.
No certificate is needed for validation; only supporting paperwork is.
There is no time limit on validation.
Failure to pass validation indicates that the product is unfit for use.
To establish the standard operating procedure, different samples are taken during validation at various intervals.
Modifications may be used to fix validation failures.
After adjustments and rerunning the activity, the validation results are acceptable.
Illustrations of calibration
- Calibration of temperature measurement equipment
- Calibration of Pressure Measuring Devices
- Calibration of Time Measuring Devices
CALIBRATION
Calibration ensures that the tool or instrument being used will produce accurate results.
Precision is ensured by calibration.
Equipment calibration ensures that the findings generated by each individual piece of equipment are accurate.
An SOP is followed for calibration.
Validation of processes and procedures is a common practice.
Typically, calibration is done on measuring tools or instruments.
Calibration is carried out as follows:
- Following the times specified by the manufacturer.
- In the event that the gadget is shocked or hit.
- The replacement of a component.
- The shift in the device’s position.
Values are compared to reference standards during calibration.
A third party normally does the calibration.
A calibration certificate is necessary for calibration.
Certificates for calibration have set expiration dates.
If calibration fails, the gadget isn’t prepared to deliver the desired outcomes.
A gadget is calibrated by being tested against several value ranges.
Repairing could be used to address calibration failure.
After the repair, the calibration results are satisfactory.
Illustrations of Validation
- Procedure verification
- Approach Validation
- Validation of Cleaning
- Program verification
- Employee verification